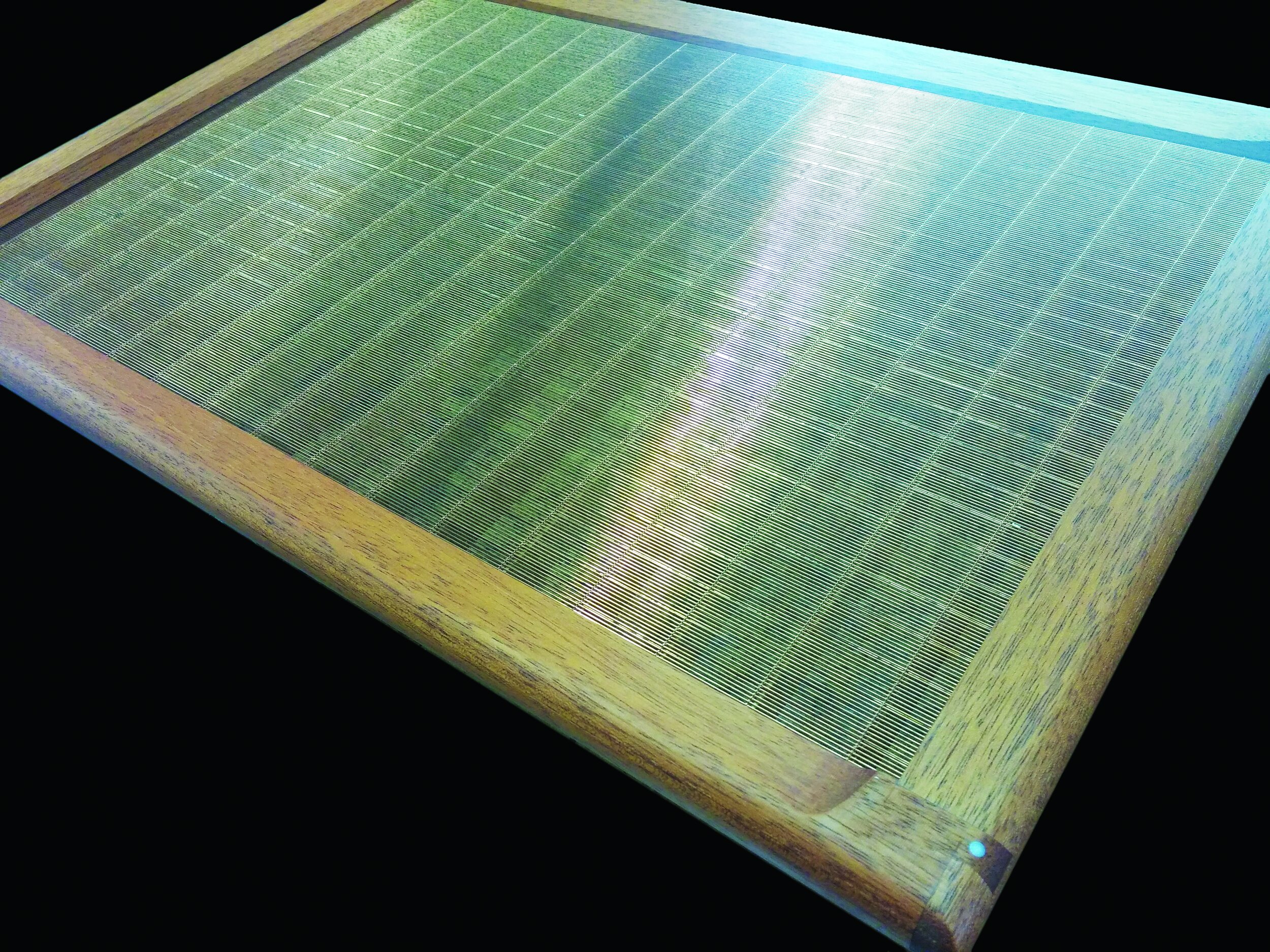
TIMOTHY MOORE
PAPERMAKING CHAMPION
Timothy Moore has individually hand built over 250 antique laid, modern laid, and wove papermaking moulds for hand papermakers. Combined with his jig- and cutting tool-making skills, and his precise attention to materials and workmanship, since 1985, Moore’s finished moulds have pleased and satisfied their new owners in four different countries, and helped advance, encourage, inspire, and perpetuate the papermaking field for 37 years. At his website, Moore continues to impact the field by generously sharing his mould-making skills and knowledge.
Timothy Moore
Essay by Cathleen A. Baker
Tim Moore is a consummate creator of moulds used to make fine paper by hand. Prior to his taking up the craft in the mid 1980s, most moulds on the market were designed for teaching papermaking in schools. They were serviceable but lacking in traditional structure, materials, and craftsmanship. (How Tim got involved in making moulds is chronicled in several publications that the reader is encouraged to read; see the end of this essay.)
By his estimation, Tim has hand-built over 257 antique-laid (single-face), modern-laid (double-face), and wove moulds for hand papermakers. Moore’s finished moulds have pleased and satisfied their new owners in several countries, and he has advanced, encouraged, and inspired the papermaking field for 37 years. Because Tim has retired from mouldmaking, he is now more interested in helping sustain the craft by freely giving information, and he hopes this will help potential mouldmakers to take up where he has left off. Via his website, Moore generously shares in minute detail his mouldmaking skills and knowledge.
When asked to detail his accomplishments, Tim included the following:
Perhaps his favorite accomplishment has been the creation of a workable, efficient loom for making wire facings and backings. Two of these have been made; the original one that served for most of his career, and a more recent, better version, a photograph of which graced the cover of Hand Papermaking in 2012.
His website exploits the digital format to present a great deal of information, including hundreds of annotated photographs detailing the processes. He intends to keep the website up indefinitely and hopes that it will prove a useful tool for other aspiring toolmakers.
For bookbinders, Tim has made 360 finishing presses, 295 signature punches, and 9 precision plows for trimming the edges of text blocks, the latter inspired by a request from Gary Frost.
He is proud of is having made tooling for producing four sizes of wooden threads with thread design based on advice from Tom Conroy. These screws are an essential part of various bookbinding presses. (Tooling was not available for these size/type threads, and so he had to make his own.) This went through several iterations; see “A Brief History of My Screw Making Efforts” on his website.
Tim has lectured and led workshops about making and understanding papermaking moulds, and taught a class on making wooden presses at the Paper & Book Intensive (PBI) at Penland, N.C., in 1997. I particularly remember the 1993 PBI in Texas, when I took Tim’s class in which we collectively created a few small laid moulds. This included the use of a miniature loom that he constructed on which we were able to weave laid wire screens. Being able to perform this task was so educational for all of the participants and resulted in a better understanding of the nuances of the patterns and marks that laid mould screens leave in the paper made on them. He has visited the University of Iowa Center for the Book (UICB) several times to deliver new moulds and book presses, using the opportunity to meet informally with students there. Most recently, he gave a workshop at the Friends of Dard Hunter (FDH) meeting at the Morgan Conservancy in Cleveland, 2012, during which the newest loom was used by attendees.
In 1981, the Friends of Dard Hunter Papermaking Museum (FDHPM) was founded, and Tim and his wife, artist Pati Scobey, attended many of the early meetings of the group. Because these meetings were small and intimate, we quickly got to know one another. When I found out that they lived in Concord, Michigan, not far from my family’s home in Grand Rapids, I was even more drawn to them, and we became, and remain, good friends. Over the years, whenever I have had questions about paper-mould construction, the very first person I (and many others I am sure) have turned to is Tim. Back in 2005, I ordered a so-called “Composite, Cutaway Mould” from Tim, which features the three screen constructions – antique laid, modern laid, and wove. (In 1987, Terry Belanger ordered the first such mould from Tim for Rare Book School when it was at Columbia University.) This was the first mould that Tim made for me, and I have used it many times when teaching paper history. I love that mould, not only because it is a great teaching tool, but also because it is so well made and a beautiful object.
A prolonged encounter with Tim occurred when I was editing and designing his contribution to Tim Barrett’s book, European Hand Papermaking: Traditions, Tools, and Techniques, which The Legacy Press published in 2018. I was struck by his ability to communicate complex concepts into words and to determine exactly which images would make those concepts clearer. It is also apparent from “Appendix C. Mould and Deckle Construction” that Tim is an accomplished problem-solver. If a tool or machine does not exist that is essential for his moving forward in crafting something, he extrapolates from examples of old models or examines the intended use of the finished product and invents a tool or machine ( as he did for the thread screws). His ingenuity and perseverance are models for us all.
Tim Moore’s knowledge about traditional papermaking moulds is astounding, generated from a decades-long study of the subject, not so much from the paltry number of books on the subject (E.G. Loeber’s work, Paper Mould and Mouldmaker, being the most comprehensive), but from his successes in replicating traditional papermaking moulds. His understanding also includes knowledge about the practice of traditional hand papermaking. He has been able to learn not only how these moulds were made but also in many cases, why. He would not call himself an expert and would freely admit and point out things that he does not know, but that is how really talented and accomplished people think of themselves.
It has been such a pleasure working with Tim over the years on several projects; I have learned so much from him and look forward to learning more. I know that there are hundreds of papermakers and bookbinders who would say the same.
Tim Moore’s induction into the NAHP Hall of Papermaking Champions is a significant and absolutely deserving acknowledgment of his remarkable life’s work in furthering our knowledge about the tools that make our understanding of the craft of fine papermaking possible.
Recommended readings:
Lee, Aimee. “The Toolmakers – Those Who Build So We Can Make. Part I: Timothy Moore and David Reina.” In Ginsberg, Tatiana, ed. Papermaker’s Tears: Essays on the Art and Craft of Paper. Vol. 1. Ann Arbor, Mich.: The Legacy Press, 2019, 208–245.
Moore, Timothy. “Appendix C. Mould and Deckle Construction.” In Barrett, Timothy D. European Hand Papermaking: Traditions, Tools, and Techniques.” Ann Arbor, Mich.: The Legacy Press, 2018, 254–290.
Moore, Timothy. “Calling All Potential Mouldmakers.” Hand Papermaking 27, no. 1 (Summer 2012): 21–25.
Moore, Timothy. “Constructing Western Molds.” Hand Papermaking 2, no. 1 (Summer 1987): 20–25.
Moore, Timothy. “A Brief History of My Screw Making Efforts.” [Blog post] (n.d.) Retrieved from: https://timothymooretools.com/a-brief-history-of-my-screw-making-efforts/
Moore, Timothy. “Directory to Mould Making Posts” [Blog post]. (n.d.) [A list of Tim’s blog posts relating to construction of moulds, deckles, and related topics.] Retrieved from: https://timothymooretools.com/2022/02/07/directory/
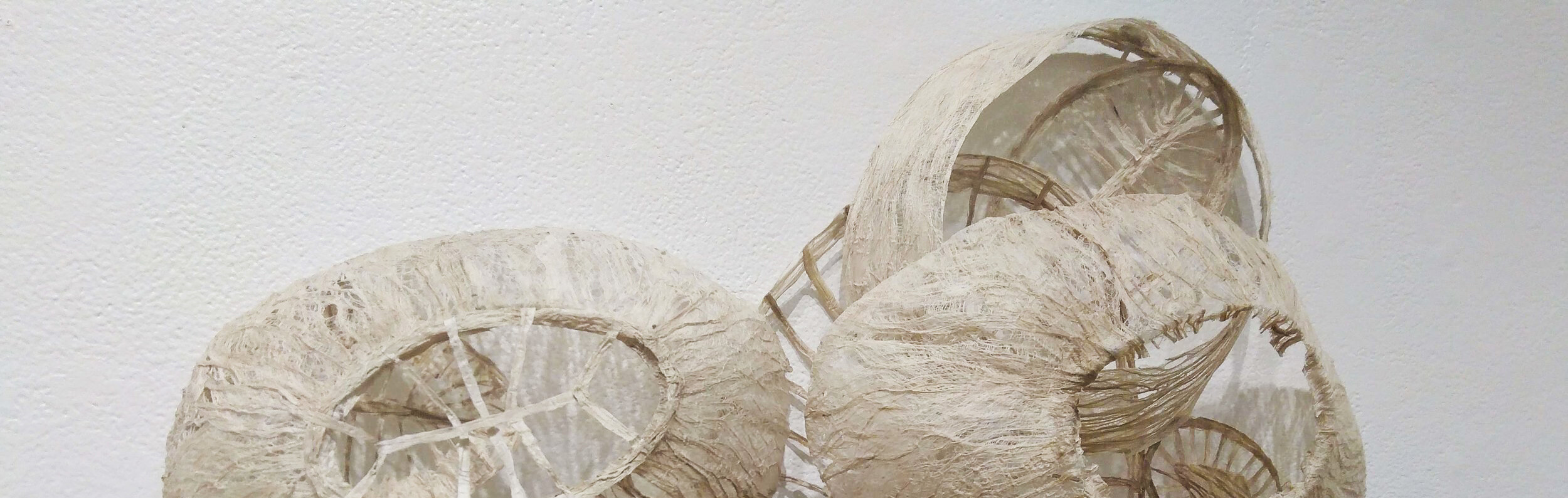
Become an NAHP Member
Join our vibrant hand papermaking community and access your membership benefits.